A giant rigging for commercial ships
At a press conference, the Chantiers de l'Atlantique presented with great pomp and ceremony the progress of their project for a sail propulsion system for ocean liners and merchant ships. The solution developed by the Nazairian shipyard is piloted by the engineer and former sailor Nicolas Abiven. It combines a sail made up of rigid panels that fold like an accordion when lowered, called Solid Sail, and an 80-metre mast that can be tilted at 70° for passage below deck, called AeolDrive.
After initial tests of the sail on a reduced scale, notably aboard Jean Le Cam's IMOCA boat and on a scale model ashore in Saint-Nazaire, the project is about to take a new step forward. An initial 25-metre demonstrator comprising the entire rigging and sail system will be installed on land from summer 2021 for testing during the winter of 2022, before the shore trials of the 80-metre, 1:1 scale version: "If the trials of the first demonstrator are conclusive, we will begin marketing the vessels as early as 2022. Our partners are already thinking about mass production," says Laurent Castaing, director of Chantiers de l'Atlantique.
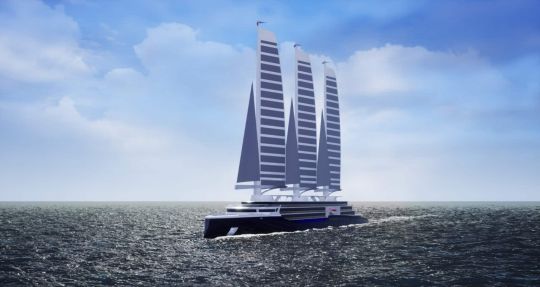
A nautical consortium for the production of the mast and sails
To carry out its project, the Chantiers de l'Atlantique turned to the yachting and ocean racing sector. The panels for the sails will be made by the shipyard Multiplast. It will be associated in consortium with CDK Technologies, Lorima, Avel Robotics and SMM technologies for the manufacture of the mast, which will be made in sleeved 24-metre sections. "In ocean racing, we have this mastery of composite materials and we are also used to working together. We know less about it, but the large trimarans of Armel Le Cléach or François Gabart are very often built with a central hull made in the yard, the floats in another and the arms in another. In the Mod70 trimaran project, we had already created this consortium to build these boats together," explains Yann Penfornis, head of Multiplast. "One mast represents 8 Vendée Globe boats in terms of carbon mass."
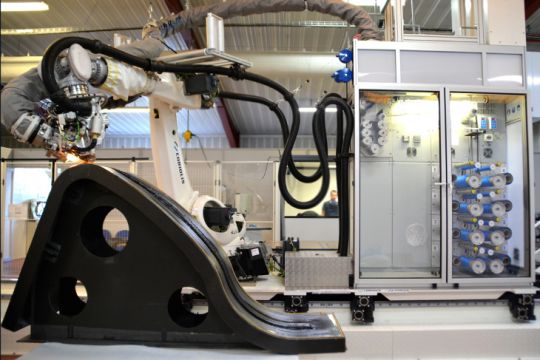
If innovation lies in development, the existing industrial tools allow the realization of the parts. "At Multiplast, we have very large ovens which allow us to bake pieces of sails without any particular investment. An element of the bottom of a sail will be 20 metres long by 6 metres wide and an IMOCA is 18.50 m long and the boats are around 6 metres wide" specifies Yann Penfornis.
A useful reflection on the durability of parts
Other partners in the project include the engineering office Gsea Design or the instrumentation specialist Pixel Sur Mer, the electronics technician Ocean Data System, the rope maker Lancelin, the rigger Blew Stoub. The riggers are also on board. The Wichard Group, owner of Lorima, is also involved through its furling system brands Profurl and Facnor. Its director, Jean-Claude Ibos, underlines the interest of the work on sustainability required for 30 years, the lessons of which could benefit yachting in return. "It's not so much about mechanical durability, because we know how steel works for that, but more about the corrosion that can happen depending on where you go sailing. And over time, we have to find the right solutions. And find, associated with this, maintenance contracts to be able to maintain the equipment over time."
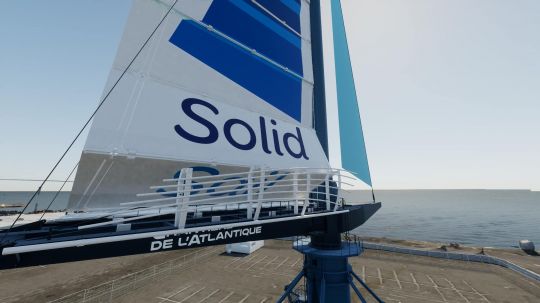
If a 200-metre long liner may seem far from yachting, we can see that the two sectors should benefit from fruitful exchanges in the years to come.