A complete mast and rigging offer
In VMG Soromap, the initials stand for Voile Mât et Gréement. They illustrate the choice of the Rochefort-based company to offer all the products necessary for the construction of a sailboat, each requiring a specific know-how. Here, with production manager Nicolas Lecuona, we focus on the manufacture of masts, spars and rigging. 9 employees work there daily, for more than 300 masts per year and hundreds of kilometers of rigging cables.
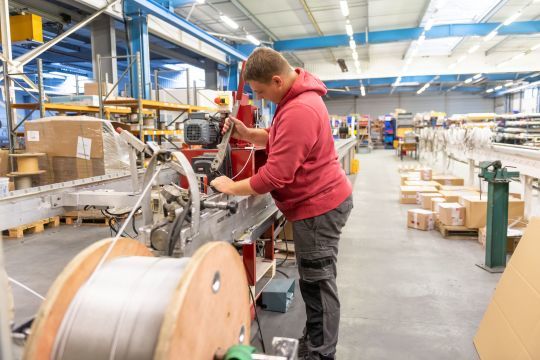
Traceability of cables and rigging accessories
VMG Soromap's expertise in rigging begins with the procurement process. The company ensures the quality of the ropes purchased from Korean suppliers for single-stranded or flexible stainless steel for standing rigging, or from other Asian suppliers for ropes. All the connecting elements and end fittings are designed in-house. Forged parts (eye / ball end) and machined parts (single threaded end / rigging screws) are produced in Tunisia within the Soromap group, in a sister company. "We have traceability on all raw materials and components purchased" explains Nicolas Lecuona.

Custom-made rigs for each boat
The rigging elements are made either from the existing rigging sent by the customer in case of identical changes, or from the cadena survey made by a salesman and rechecked by the internal office or from the plans of the new boat. Professional riggers have a configurator to automatically generate their orders.
"Then, an internal production order is issued from the customer orders. It includes a descriptive sheet of the rig with its elements, forestay, shroud, cap shroud, etc., as well as a list of parts to be taken out of the warehouse and finally a certificate of conformity." explains the production manager.
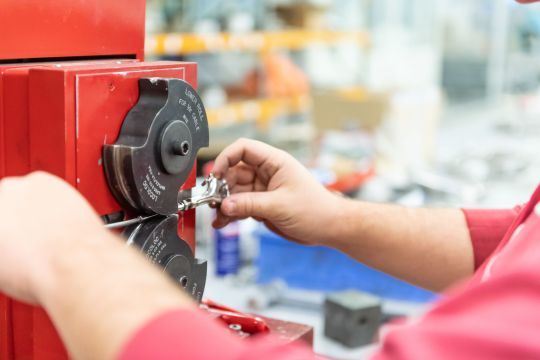
The operator cuts the cables to the right length and crimps them according to the internal procedure. Each cable is then put through the tensile test bench to validate the crimping quality, by loading it up to 10 to 15% of the breaking load. He checks the length of the cable. "The employee then signs the certificate of compliance before sending it to the customer" underlines Nicolas Lecuona.
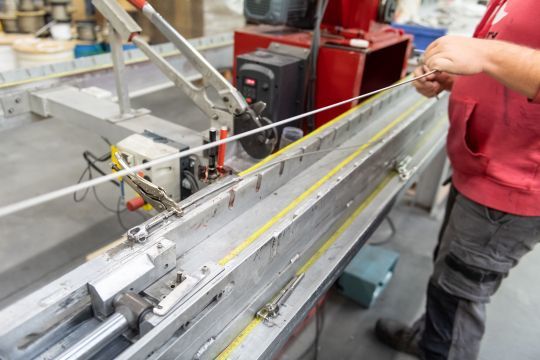
The product is then shipped worldwide, with packaging adapted to the destination, by the logistics department of VMG Soromap.
Exclusive mast profiles
Designed in the VMG Soromap design office, the manufacturer's masts are entirely exclusive to it. It has its own dies allowing the production in Europe of extruded aluminum profiles according to its needs. "They come to us already anodized to have an industrial quality treatment. We then store them in a dedicated area, handling them with straps to avoid damaging them." explains the manager.
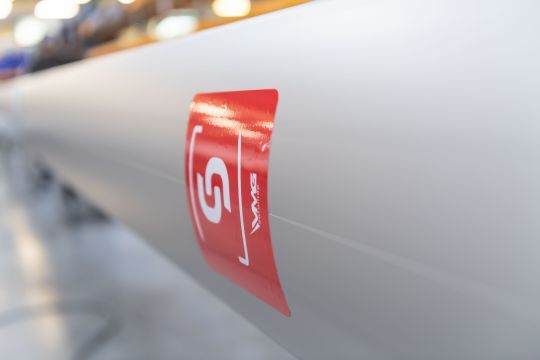
The forged products are made in Soromap's Tunisian subsidiary, while the stainless steel microfusion elements are made in subcontracting in VMG Soromap's own molds.
Machining and fitting of masts
Production can then begin, after a visual check of the mast, followed by a geometric check. "We check for straightness, twisting... directly on the machining center, which is a precise marble. We have two machining centers: a four-axis, 18.5-meter long and a five-axis, 23-meter long." says the mast specialist.
Once machined, the mast is degreased and deburred by hand. "This allows us to check the machining." says the manager.
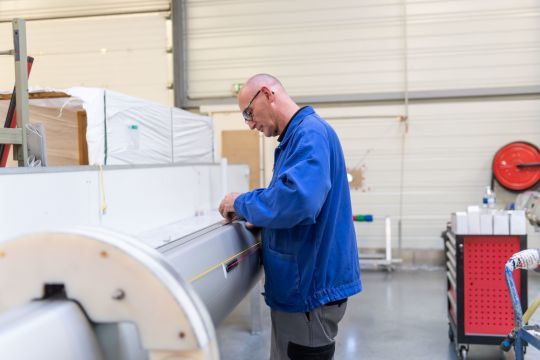
The operators then place the iro tubes, the sheaths for the cables. At the same time, a person in the store prepares all the fittings to be mounted on the mast. "The assembly on the mast takes 4 to 12 hours depending on the complexity, for example if there is a sleeve for export shipments. Then, the workshop manager checks the mast with a decameter, verifies that the parts are in the right place and the seamanship is done where it should be, that there are no scratches or anomalies, and he signs the work order, as well as the operator." concludes Nicolas Lecuona.
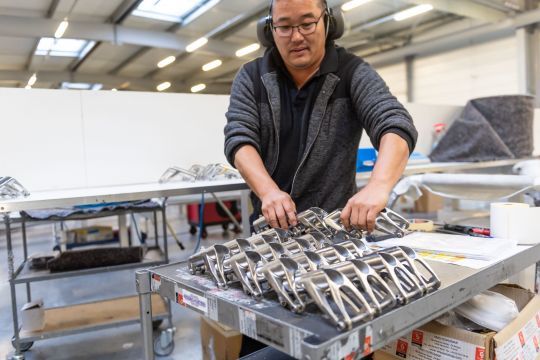
Adapting to the customer
VMG Soromap adapts to the customer's needs in terms of finishing and shipping conditions.
A 25-meter paint booth allows us to offer a choice of lacquer or paint colors with the help of Soromap SPV, the subsidiary that produces and formulates its own products. The TIG boilermaking workshop is in charge of making masthead swages for yachtsmen looking for lightness in their tops.
Ringed tubes protect the masts that are sent for export.
Thanks to its experienced team, VMG Soromap is able to meet the demands of its customers, concentrated around its core business, sailboats from 20 to 60 feet.