Recycle carbon in a mechanical way
Involved in the composite industry since his graduation from the Ecole des Mines, Benjamin Saada immediately co-founded Expliseat in 2011, the company behind the aircraft seat considered the lightest in the world at the time. He then logically became interested in carbon fiber recycling and noted that existing solutions were mainly through pyrolysis or solvolysis. "The solution emits more CO2 than the production of virgin fibers and 80% of the waste always ends up in landfill or incineration" he regrets.
In October 2020, it launched Fairmat to find a research and development solution for managing this carbon fiber waste. The process results in a fully mechanical, mainly cold, very high precision cutting of the fibers. It maintains the high performance mechanical characteristics. "The bending and strength curves are much higher than the average for recycled materials," says Benjamin Saada.
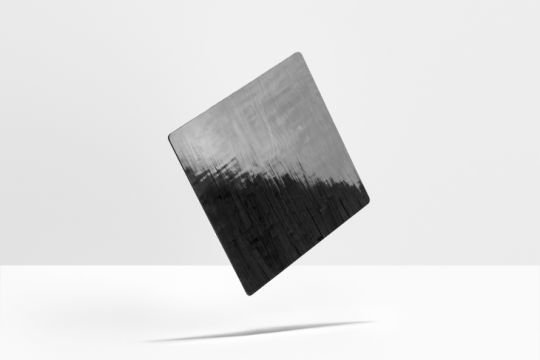
Customized materials to replace fiberglass
The recovered elements are then robotically assembled by adding virgin resin. Fairmat thus optimizes the positioning and obtains a customized product that meets the customer's needs in terms of mechanical performance.
The finishes, painted or glossy, are chosen by the customer.
The applications are multiple, in furniture or in soft mobility such as cargo bike bodies or for applications in the electric vehicle. "In the nautical industry, we can imagine for example roofs with Fairmat materials. Weight is a real issue in the boating industry. We are not in competition with carbon, but we can replace fiberglass, thanks to a low cost, energy balance and our short circuit based on local waste. We can be up to 30% cheaper and twice as light as aluminum," says Fairmat's founder
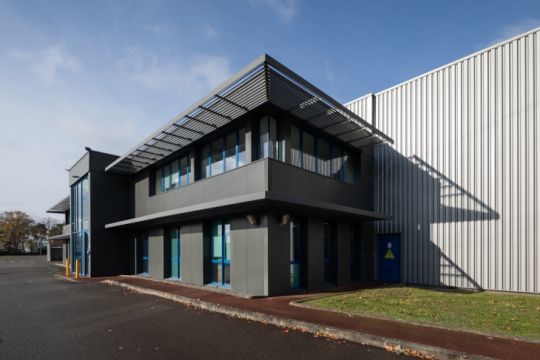
Industrialization in progress
Agreements with major players in the production of composite materials such as Hexcel or aeronautical manufacturers to recover material have enabled Fairmat to accelerate its development. A new plant in Bouguenais has started production to begin the transition to the industrial phase. It should eventually be able to produce 5000 tons of material per year.