Jérôme de Metz, CEO of the Bénéteau Group, answers BoatIndustry's questions on the industrial and human resources strategy of the heavyweight in the marine industry. He talks about the progress of the brand portfolio reorganization.
After closing plants in 2020, you have announced investments in the Jeanneau site in Cholet. Can you tell us more about your choice of industrial facilities?
We have to take a chronological approach. We first needed to adapt our production capacity for large boats, when the economic crisis arrived following the health crisis. At the time, our only reference point was the last major crisis in 2008. We made the choice to prepare for the worst, i.e. the same as in 2008. Out of the 19 boat factories, we made an industrial plan to determine how many factories to close or mothball, in the end 2 or 3. Some sites had no future because some were already not operating at 100%. At Marion, in the United States, a lot of investment would have been needed, and the site was already in difficulty because of the monohull market in North America. For Seascape in Slovenia, which employs only 40 people, the managers took over the majority and we went into subcontracting with a start-up management style.
At the same time, as the season progressed, we saw a strong demand for small boats and a smaller than expected drop in the rest. The challenge today is to have fewer, more saturated factories. To improve the productivity of our factories, we are investing in France and we are proud to say so. There has never been any question of disinvesting in France. We invested 14 million euros last year for the extension of the Saint-Gilles Croix de Vie plant. By modernizing the park in Cholet (editor's note: 5 million euros of work between now and October 2021 on a plant with 290 employees), we are moving from 1 axis to 3 axes, with more flexibility and a move from 2 boats per day to 2.5 boats per day.
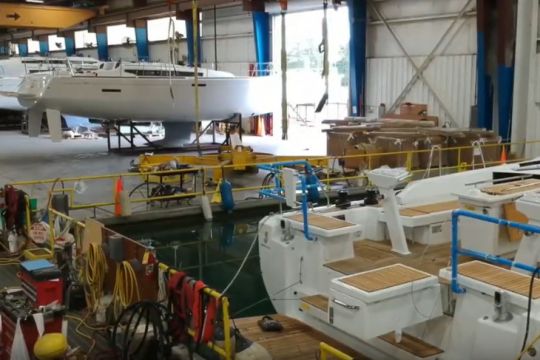
What about locations in relation to logistics and the market served?
There is a refocusing in France, but boats under 35 feet are still built in Poland. The job pool there is quite saturated. We are not the only ones producing there, our competitors are too, and one day Poland will probably be insufficient. We are thinking about our industrial footprint in 3 or 4 years. Apart from Cadillac (editor's note: Bénéteau's last factory in America), we are far from the North American market. We remain competitive with production in Poland, but there is a question of logistics and ecological reasonability. We are committed to the Neoline project (editor's note: a sailing cargo ship project supported by Bénéteau), but beyond that, the USA issue is not addressed. There is a lot of room for development in this market and it is a topical issue in our 5-year plan, which has been drawn up in a rolling manner according to the 23 market segments we have identified.
In Asia, there is an evolution, but no revolution. We do not see a rapid take-off, apart from the catamaran fleets for local and international tourism as soon as the planes take off again. There are also inland waters, depending on the environmental awareness of the Chinese. The problem of choosing an industrial location is complex. It is very different from America, because there are many countries with protectionist barriers.
After the sale of CNB, how is the process going for the other brands you wanted to sell in the Let's Go Beyond plan (Monte Carlo Yachts, Glastron and Scarab)?
There are discussions. We are not in a hurry. The business is good and we don't have a sword in our back. We are not ashamed to have them!
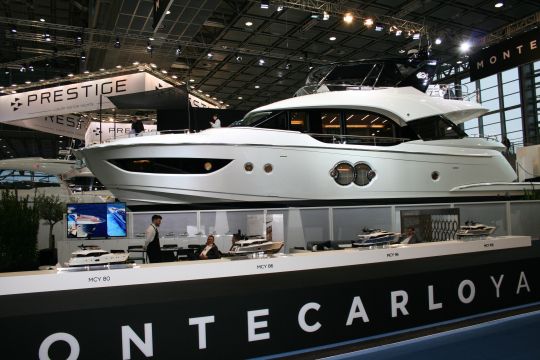
What is the situation in terms of recruitment, in terms of new hires, work-study programs, and also the mobility of employees from closed plants?
We recruit between 200 and 500 people per year. There are about 200 retirements per year. During the Gastinel period (editor's note: the group's previous leader until 2019), there were 200 to 300 new jobs created, but the growth was not sufficient to finance these investments. We have started recruiting again. There is no longer any short-time working. Most of the internal transfers following the closure of the Chalans and Herbaudière plants have been accepted. We had 2,000 temporary workers not so long ago and we are starting to recruit again.
Concerning the alternation, it is one of the great pride of the group. We have never interrupted them. It is a civic duty to train young people and we are always happy to hire the people we have trained. The retention rate is high.