A thermochemical process for recycling composite wastes
The Korec company, based in Tuscany, has developed an innovative system for recycling composite objects, such as boats and leisure equipment. Based on a thermochemical process, the solution allows the depolymerization of the resin. By heating at high temperature and adding CO2 , the glass fibres are separated from the liquid. In a final step, the thin "burnt" layer on the fibres is removed, allowing them to be reused. The recovered liquid can then be reused, mixed with conventional resins. Korec claims to obtain a recovery yield of 99% of the fiber mass and 85% of the resin mass. "The system works with orthophthalic and isophthalic polyester resins, as well as vinylester. We have also tested the process on waste mixed with different resins, as well as sandwiches with pieces of wood or PET cores and gelcoat as found on boats. In all these tests, the liquid retains a similar level of polymerisation, regardless of the type of resins present in the original waste," explains Laura Saviano. Tests are also conducted with carbon fibres and epoxy resins.
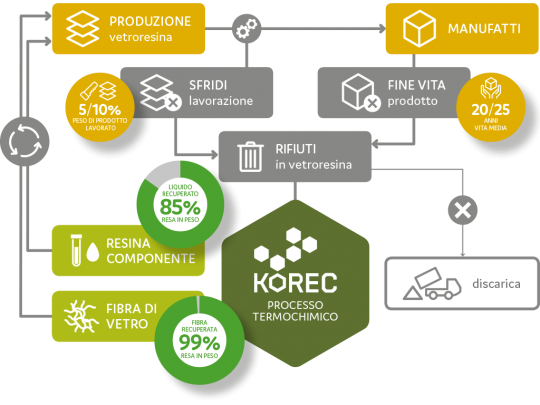
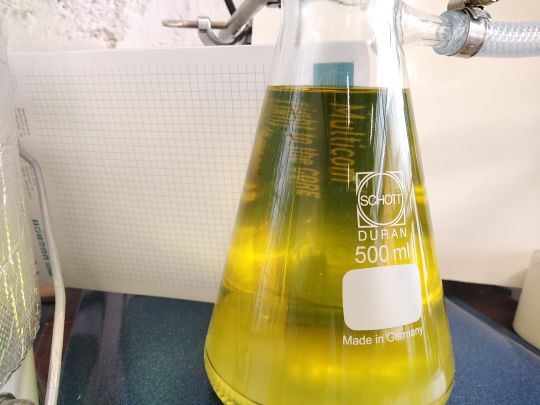
New parts for boats made from used resin
To validate its concept, Korec produced several parts from resins mixed with its recovery liquid. If they are not complete boats, composite storage units or camper roofs have been laminated and have successfully passed mechanical and aging tests. "Tests with Korec's recovery liquid between 10 and 20% showed mechanical characteristics equivalent to new resins, in terms of stiffness, flexural strength, tensile and compressive strength," says Laura Saviano.
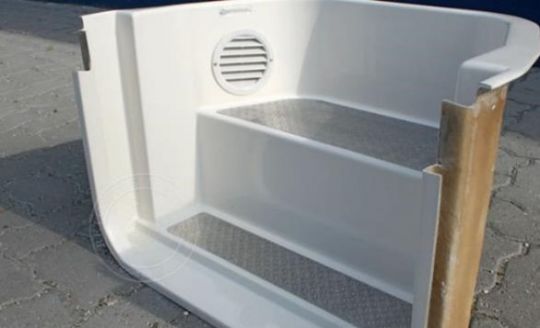
Moving to industrial scale
On trial since 2019, Korec indicates that its process is now mature. A first plant is scheduled to open in March 2021 for industrial-scale composite recycling. To guarantee the profitability of the equipment, a minimum of 500T must be processed per year. Given the low cost of the fibers and the energy required for treatment, the viability lies in the recovery of the liquid. "With a resin price between 1500euros/T for orthophthalic resins and 6000euros/T for vinylesters, the process becomes profitable. Our objective is to disseminate the process through patent licenses and the delivery of turnkey plants. This could be for resin manufacturers or large composite producers who would use the liquid directly" concludes Laura Saviano.