Livrea yachts : 2 modern partners to reinvent the heritage
Livrea Yachts was founded by two young Italians, Francesco Belvisi and Daniele Cevola. Their initial goal was to save a boat from the heritage of their island of Pantelleria, the lancia pantesca. Not being carpenters themselves, they decided to adapt the design and use modern technologies for this boat. This is how 3D printing is invited into the project and Livrea 26 is launched, supported by CRP Technologies, a company active in Formula 1. If Hanse announces the printing of the hull as April fool's joke, for Livrea, it's concrete.
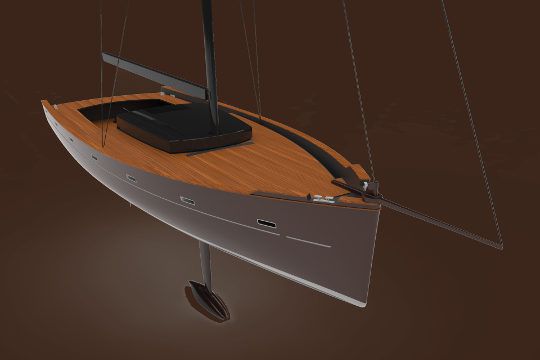
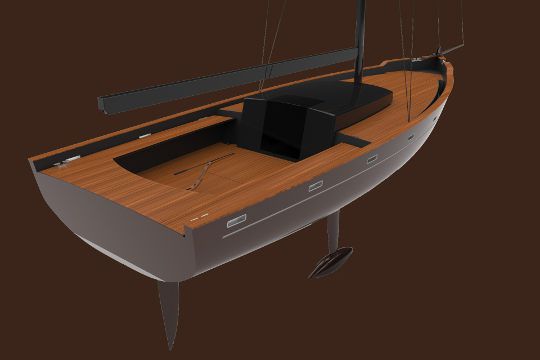
Complex parts in one operation
The traditional boat revisited obviously has an Italian design. Exit thus the sheets on bridge, they run in the thickness of the material. Instead of integrating PVC tubes into foam, the sandwich core is printed in 3D, integrating from the start the passage of the string, but also details such as drainage. In one operation, the finished part is obtained, saving operator time and cost. Other parts, such as mast footways or instrument holders, are thus made on Booka 26.
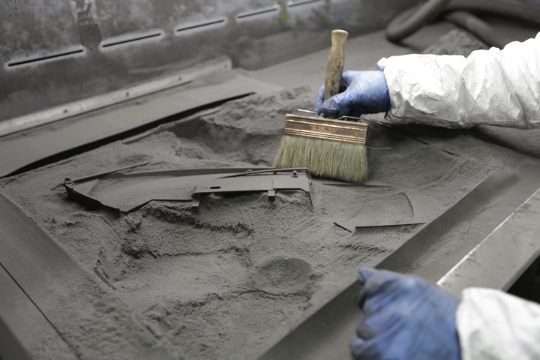
Ease of construction and design freedom
The use of carbon-filled polymers results in a sandwich core with superior mechanical properties to conventional PVC foams. Their stiffness allows constructions without moulds, facilitating manufacturing.
The strength properties of the new materials allow an optimization of the structure. For this, a partnership with Autodesk provides Livrea with an optimization software used in aeronautics.
3D printing allows the material to be placed only where it is useful, leaving great design freedom. Kuka Roboter provides Livrea with a robot to deposit the material in areas inaccessible with a conventional 3D printer.
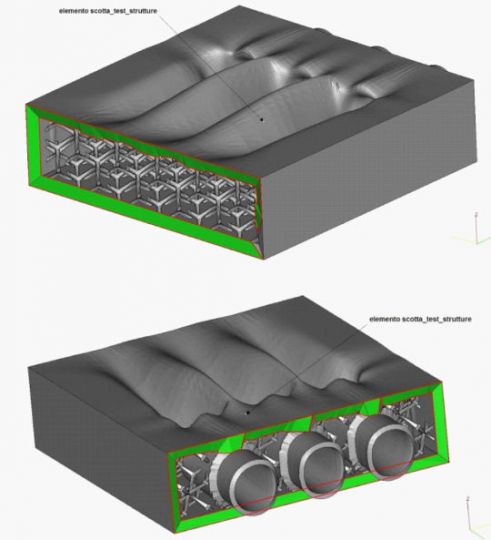
Subcontracting of parts, complete boats: many perspectives
The current cost of 3D printing reserves it for boats with high added value. The one-off market is the main target in boating. Nevertheless, complex series parts are also of interest to large projects that have made contact with Livrea. Subcontracting is a development axis.
The two partners are now working on the construction of parts several metres long. The ultimate goal is of course the manufacture of entire boats with 3D printers. If the democratization of 3D printing in the nautical industry is not yet a reality, it is coming back at a snail's pace!